LED lights have become increasingly popular due to their energy efficiency, long lifespan, and environmental benefits compared to traditional incandescent bulbs. But have you ever wondered why your LED lights stay cool to the touch even after hours of operation? Or why LED lights last much longer than traditional incandescent bulbs? The answer to these questions lies in a small, yet crucial component called the LED heat sink.
What is a LED Heat Sink?
A LED heat sink is a device designed to absorb and dissipate heat generated by the LED chips. It is typically made of thermally conductive materials like aluminum or copper and is shaped to fins or other geometries to maximize its surface area for effective heat transfer to the surrounding air. The heat sink is crucial for maintaining optimal LED performance, efficiency, and lifespan.
Do LEDs Produce Heat?
Although LEDs are much more energy-efficient than traditional lighting sources, they still generate heat during operation. The heat is generated at the junction where the LED chip meets the circuit board, as a result of the inherent inefficiencies of the semiconductor materials.
This causes the junction temperature (Tj) to increase, leading to a decrease in the LED’s brightness and efficiency. High temperatures can also shorten the lifespan of the LED by causing it to deteriorate faster over time. Gradual loss of brightness is a common sign of LED deterioration rather than a sudden failure. To prevent this, it’s important to keep the LED’s junction temperature low and avoid overdriving the LED with more current than it is rated for.
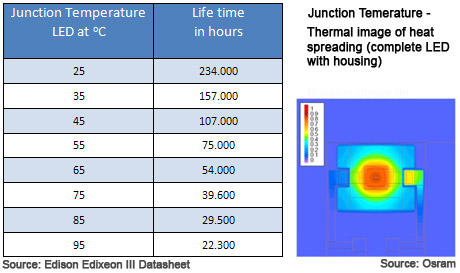
The radiant efficiency of LEDs, which refers to the ratio of total optical output power to total electrical input power, is usually between 5 and 40%. This means that a significant portion of the input power is lost as heat. The Tj of the LED is hotter than the surrounding environment when it is operating. To dissipate this excess heat, the heat flows through various components such as the solder, MCPCB, and heat sink, as illustrated in the diagram below.The most important part of LED cooling is the thermal path from the LED junction to the outside of the light fixture. Heat needs to be conducted away from the LED in an efficient manner, and then removed from the area by some sort of cooling or dissipation. It is why we need LED heat sink.
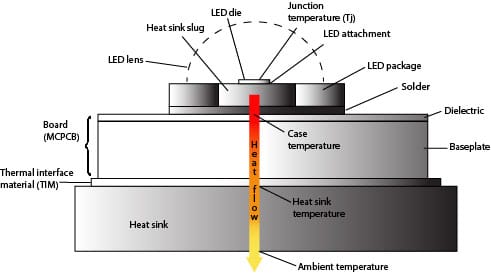
Source: vektrex
Why should we dissipate heat generated by LEDs?
Dissipating heat generated by LEDs is crucial for managing junction temperature, which impacts several key aspects:
- LED Efficiency: LED efficiency is affected by junction temperature. As the temperature increases, LED efficiency decreases, causing a reduction in emitted light for the same input power. A study by P. Pust et al. (2015) showed that a junction temperature increase of 30°C (from 25°C to 55°C) can cause a decrease in LED efficiency of up to 10%.
- Color Shift: LED color output is influenced by junction temperature. Higher temperatures can cause chromaticity shifts, resulting in color changes. This is particularly important for applications requiring precise color rendering. The color shift is more pronounced in phosphor-converted white LEDs, where a higher junction temperature can cause a shift towards the blue end of the spectrum.
- Reliability and Lifetime: LED lifetime is significantly impacted by junction temperature. Higher temperatures can cause accelerated aging, reducing the LED’s overall lifespan. According to the Arrhenius equation, the rate of a chemical reaction doubles with every 10°C increase in temperature. A study by Narendran et al. (2008) found that an increase in junction temperature from 80°C to 120°C can result in a 50% reduction in LED life.
- Thermal Management: Effective thermal management is vital for maintaining LED performance and reliability. This includes the use of heat sinks, thermal pads, and thermal interface materials to dissipate heat generated by the LED efficiently. Proper thermal management helps preserve the LED’s performance characteristics, such as light output and color stability.
In conclusion, dissipating heat generated by LEDs is vital for ensuring LED efficiency, color stability, and reliability, as well as prolonging their lifespan. Implementing proper thermal management techniques, including the use of heat sinks, is crucial for optimizing LED lighting system performance and longevity. Factors such as electrical and thermal design, ambient temperature, and heat dissipation effectiveness can influence the junction temperature of a LED. By optimizing these factors, it is possible to minimize the junction temperature and enhance the performance of the LED.
Why Is LED Heat Sink Important?
LED heat sinks play a critical role in managing the heat generated by LEDs. They help:
- Enhance efficiency: By effectively dissipating heat, heat sinks prevent the LED from reaching high junction temperatures, maintaining its energy conversion efficiency and light output.
- Increase lifespan: Proper heat management prolongs the lifespan of the LED, ensuring reliable performance for many years.
- Reduce safety risks: Excessive heat can cause LEDs to fail prematurely, potentially resulting in fire hazards or other safety concerns. Heat sinks minimize these risks by keeping the LED at a safe operating temperature.
How Does LED Heat Sink Work?
A LED heat sink works through a process called heat transfer. It absorbs the heat generated by the LED and transfers it to the surrounding environment, typically through a combination of conduction, convection, and radiation.
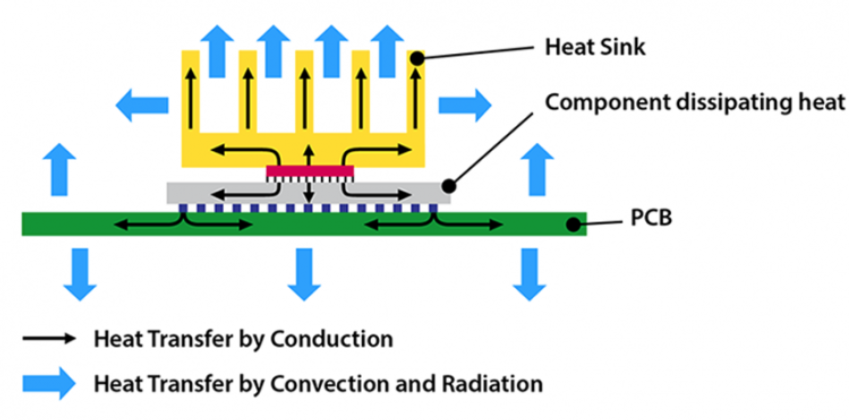
- Conduction: Heat is transferred from the LED to the heat sink through direct contact between the two surfaces. The heat sink material must have high thermal conductivity to facilitate this process.
- Convection: The heat absorbed by the heat sink is dissipated into the surrounding air through natural or forced convection. Natural convection relies on the air’s movement due to temperature differences, while forced convection uses fans or other external devices to enhance airflow.
- Radiation: Some of the heat absorbed by the heat sink is emitted as infrared radiation, which also helps to cool the LED.
What are the Different Types of LED Heat Sinks?
LED heat sinks can be broadly classified into three categories: Passive Cooling, Active Cooling, and Hybrid Designs. Each category has various types of heat sinks that offer unique benefits depending on the application and environment.
Passive Cooling
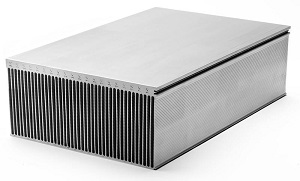
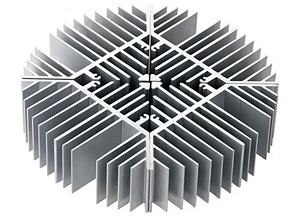
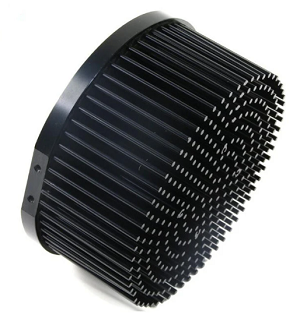
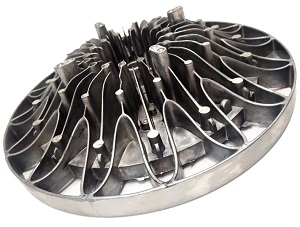
Passive heat sinks rely on natural convection to dissipate heat. They are quieter and more energy-efficient than active cooling solutions but may be less effective in high-power applications or confined spaces.
- Pin fin heat sinks: These heat sinks feature an array of thin, cylindrical pins that extend from the base, providing a large surface area for heat transfer. Pin fin heat sinks are suitable for situations where airflow is multidirectional.
- Plate-fin heat sinks: These heat sinks consist of a base plate and a series of fins, providing a large surface area for heat dissipation.
- Extruded heat sinks: Extruded heat sinks are made by extruding aluminum into a specific shape and size, creating a finned structure that increases the surface area for heat dissipation.
- Bonded fin heat sinks: These heat sinks consist of a base material and fins bonded together using a high-strength adhesive, improving heat transfer efficiency and reducing thermal resistance.
- Folded fin heat sinks: Made of thin metal fins that are bent and stacked together, creating a large surface area for heat dissipation in a compact and efficient cooling solution.
- Straight fin heat sinks: Straight fin heat sinks have a series of parallel plates or fins extending from the base. They are designed to work with unidirectional airflow and are typically used in conjunction with fans.
- Die-cast heat sinks: These heat sinks are made using a die-casting process, where molten metal is forced into a mold under high pressure. Die-cast heat sinks can have complex shapes and integrated features, but they may have lower thermal performance due to the presence of air bubbles or voids.
- Z-Clip Retainer Heat Sinks: Z-Clip Retainer Heat Sinks are a type of heat sink that features a Z-shaped clip to secure the heat sink to the LED light source. This design allows for efficient heat dissipation while maintaining a strong connection between the LED and the heat sink.
Heatsink Type | Material Type | Workmanship | Surface Treatment | Heat Conductivity |
Pin Fin Heat Sink | AL1070 or other pure aluminum, high heat conductivity (226~237w/m.k) | Cold Forging | Anodizing and pigment excellent | No air or void inside, no thermal resistance |
Straight Fin Heat Sink | Aluminum alloys, such as AL6063, moderate heat conductivity (155w/m.k) | Hot Extrusion | Anodizing and pigment good | Air bubble or void existed, thermal resistant |
Die-Cast Heat Sink | Die casting aluminum alloy, poor heat conductivity (96w/m.k.) | Permanent Mold Die Casting | Not suitable for anodizing | Air bubble or void existed, thermal resistant |
Active Cooling
Active cooling heat sinks use fans or other external devices to enhance airflow, improving heat dissipation. They can handle higher heat loads but may generate more noise and consume more power.
- Forced-air heat sinks: These heat sinks are designed to work with fans or blowers that force air across the fins, increasing the rate of heat dissipation.
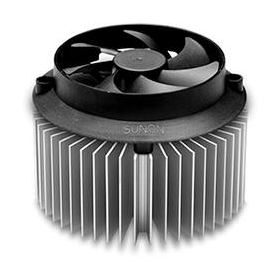
Hybrid Designs
Hybrid heat sinks combine features of both passive and active cooling systems, as well as additional elements, to optimize their performance.
- Heat pipe heat sinks: These heat sinks utilize heat pipes to transport heat away from the LED, combining passive cooling with the enhanced heat transfer capabilities of heat pipes.
- Vapor chamber heat sinks: Vapor chamber heat sinks use a thin chamber filled with a liquid that evaporates and condenses to dissipate heat, improving thermal performance compared to traditional solid metal heat sinks.
- Phase change material (PCM) heat sinks: These heat sinks incorporate phase change materials that absorb and release heat as they change states (solid to liquid or vice versa), providing additional heat storage and dissipation capabilities.
- Cold plates: Cold plates are cooling systems designed for LED lighting fixtures that dissipate heat generated by the LEDs and maintain optimal temperature levels. They are made of aluminum, copper, or a combination of both and work by conducting heat away from the LED and dispersing it into the surrounding air.
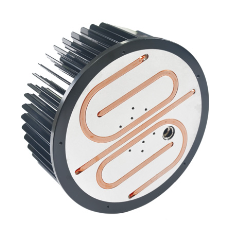
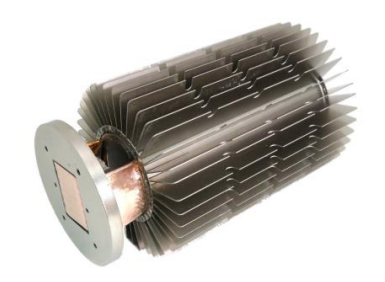
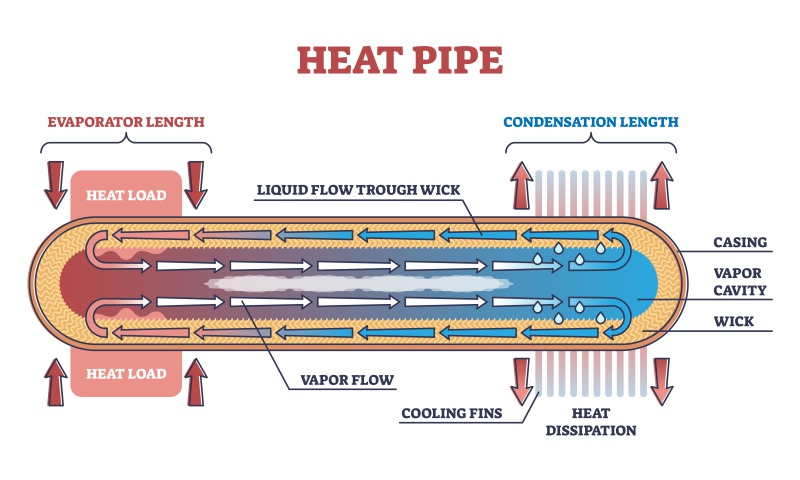
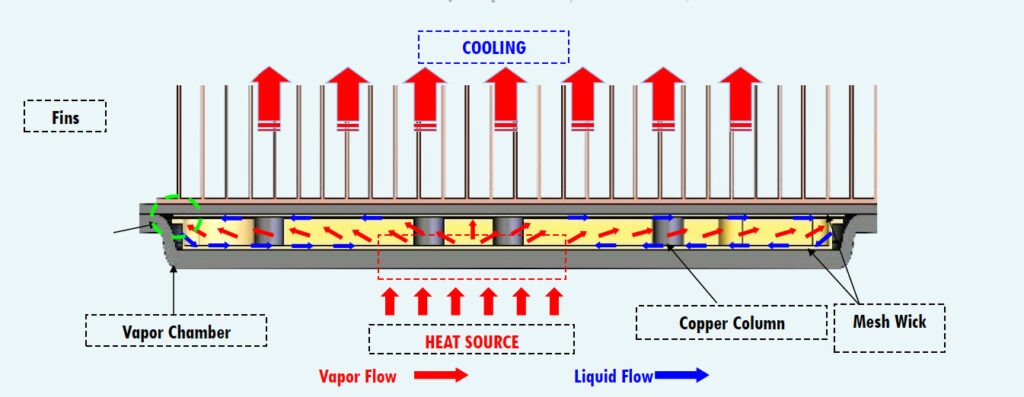
LED heat sinks are crucial components in LED lighting systems, ensuring optimal performance, efficiency, and longevity. This comprehensive guide will cover various aspects of LED heat sinks, including material selection, design considerations, and proper installation. By understanding the importance of heat sinks and how they work, you can make informed decisions when choosing LED lighting solutions for your home or business.
Which Materials Are Commonly Used for LED Heat Sinks?
An effective LED heat sink must be made from materials with specific properties. These materials should have high thermal conductivity and a high radiation coefficient to facilitate efficient heat transfer. The heat sink’s surface area should be large enough to ensure proper heat dissipation. In addition to these thermal properties, heat sink materials should also be lightweight, easy to process, and affordable. The most common materials used are aluminum and copper, each with its advantages and drawbacks.
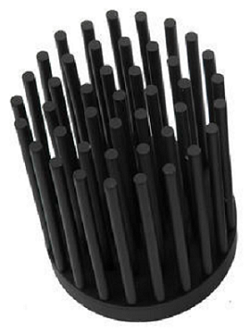
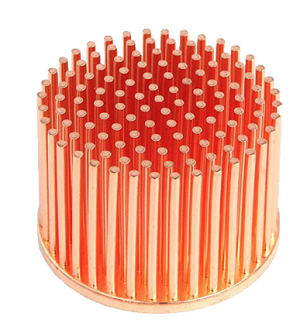
- Aluminum heat sinks: Aluminum is a popular choice for heat sinks due to its lightweight (2.7 g/cm³), low cost, and good thermal conductivity (approximately 237 W/m·K). It is also corrosion-resistant and can be easily extruded or forged into various shapes. Common aluminum alloys like AL6063 provide sufficient hardness for heat sink applications. Aluminum heat sinks often use extrusion technology, with the Pin-Fin ratio (height of fins divided by the distance between adjacent fins) as an indicator of effective heat dissipation area and advanced extrusion techniques.
- Copper heat sinks: Copper has a thermal conductivity of about 400 W/m·K, which is 1.69 times that of aluminum. This allows copper heat sinks to dissipate heat more quickly. However, copper is heavier (8.96 g/cm³), more expensive, and more challenging to process. Pure copper heat sinks, made from oxygen-free copper (with a copper content of more than 99%), offer better thermal conductivity than lower copper content alternatives (such as phosphorus copper with a copper content of less than 85%).
- Copper-Aluminum Hybrid Technology: Some high-end heat sinks use a copper-aluminum hybrid manufacturing process, with copper bases for quick heat absorption and aluminum fins for complex shapes and larger heat storage spaces. This approach combines the advantages of both materials, providing a balance between cost, weight, and thermal performance.
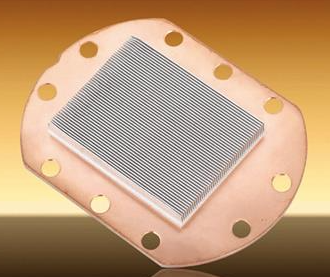
Other materials occasionally used for specific LED applications include:
- Graphite: Graphite can be used in LED heat sink applications requiring lightweight and flexible materials. With high thermal conductivity, it can be suitable for certain niche LED applications.
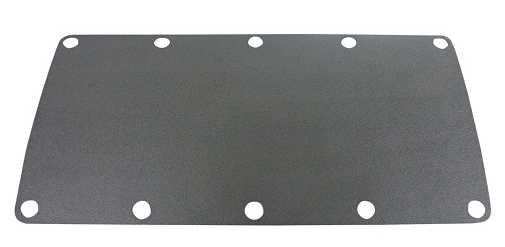
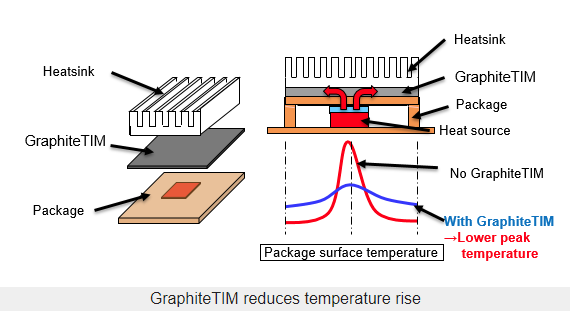
- Thermally Conductive Plastics (Polymers): Thermally conductive plastics, like certain polyamide (PA) composites, can be used for low-temperature or low-power LED heat sinks. They are lightweight, easy to mold, and offer good electrical insulation properties, but have lower thermal conductivity than metals.
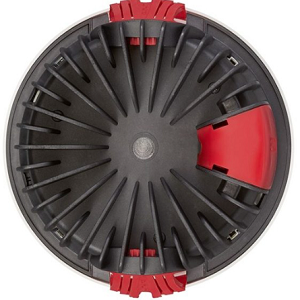
- Ceramics: Ceramic materials, such as aluminum nitride, are used in LED heat sink applications requiring excellent electrical insulation properties along with thermal conductivity. They can be useful in high-frequency or high-voltage LED applications.
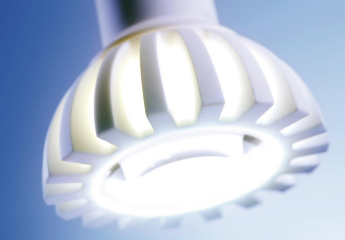
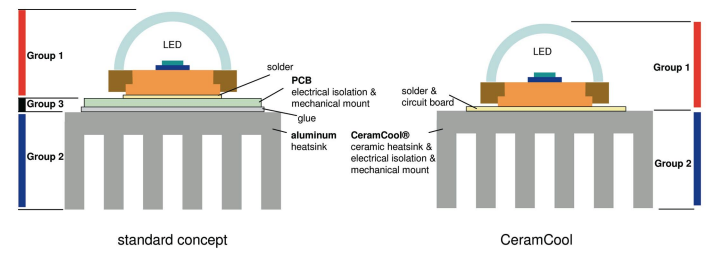
What to Consider When Picking A LED Heat Sink?
When selecting and designing a LED heat sink, consider the following key factors to ensure optimal performance and compatibility:
- Thermal Performance: Ensure the heat sink can effectively dissipate the heat generated by the LEDs by selecting one with a low thermal resistance that meets or exceeds the requirements of your LED system. For example, a high-power LED with 10W output may require a heat sink with a thermal resistance of 3°C/W or lower.
- Size and Weight: Choose a heat sink that fits within the space constraints of your application and does not add excessive weight. For instance, a small LED system may require a heat sink no larger than 50mm x 50mm x 20mm. The shape, size, and orientation of the fins play a significant role in the heat sink’s thermal performance and should be optimized for the specific application and airflow conditions.
- Cost: Balance the cost of the heat sink with its performance and the overall budget for your project. Selecting a material with a good balance of thermal conductivity and affordability, such as aluminum (with thermal conductivity around 237 W/m·K), can help optimize the cost-performance ratio.
- Compatibility: Make sure the heat sink is compatible with your specific LED system, including the LED type, PCB, and mounting requirements. For example, if your LED system uses an MCPCB, ensure the heat sink can accommodate the PCB’s dimensions and mounting holes.
- Heat Flow and Thermal Conductivity: Proper design and material choice can ensure optimal heat flow, leading to better heat dissipation. Higher thermal conductivity materials, such as copper (with thermal conductivity around 400 W/m·K), are more effective at dissipating heat but may be more expensive and heavier than aluminum.
- Natural Convection and High Heat Dissipation: To achieve high heat dissipation, a heat sink must be designed to maximize its surface area, optimize fin geometry, and use materials with high thermal conductivity. Passive cooling solutions rely on natural convection, where the heat sink dissipates heat without the use of fans or other external devices. Design aspects, such as fin geometry and surface area, play a significant role in enhancing natural convection. For example, a pin fin heat sink with a pin-fin ratio of 5:1 can provide up to 50% more surface area for heat transfer compared to a straight-fin heat sink with the same base dimensions.
- Corrosion resistance: Materials with good corrosion resistance, such as aluminum, can extend the lifespan of the heat sink and maintain its performance over time.
- Machinability: Some materials, like aluminum, are easier to machine and form into complex shapes, which can result in more efficient and cost-effective manufacturing processes.
By considering these factors, you can design and select an LED heat sink that effectively manages heat, ensuring the longevity and reliability of your LED lighting system.
MCPCBs: How Do They Help the LED Heat Sink?
Metal Core Printed Circuit Boards (MCPCBs) play a critical role in enhancing the efficiency of LED heat sinks. MCPCBs are PCBs with a metal core, typically aluminum, that provides excellent thermal conductivity and heat dissipation. By using an MCPCB, the LED and its associated components are mounted on a thermally conductive substrate, allowing heat to spread evenly and efficiently across the board, ultimately reaching the heat sink for dissipation.
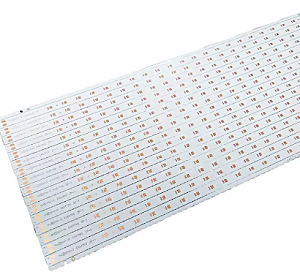
The use of MCPCBs offers several advantages in LED lighting systems:
- Improved thermal performance: By effectively conducting heat away from the LED, MCPCBs help prevent overheating and extend the lifespan of the LED.
- Compact design: MCPCBs are designed to be lightweight and compact, allowing for more efficient designs in LED lighting systems.
- Better heat distribution: MCPCBs ensure uniform heat distribution across the entire board, reducing hotspots and promoting efficient heat transfer to the heat sink.
- Enhanced reliability: As MCPCBs help maintain optimal LED temperature, the overall reliability of the lighting system is improved, reducing the likelihood of premature failure.
Why Does the Weight of the Heat Sink Matter?
The weight of the heat sink has implications for the overall performance and practicality of a LED lighting system. While heavier heat sinks may offer better thermal performance due to increased mass and surface area, they can also:
- Strain supporting structures: Excessive weight can put stress on the supporting structures, necessitating reinforcement or more robust materials, which can increase overall costs.
- Increase shipping costs: Heavier heat sinks can result in higher shipping costs, impacting the project budget.
- Make installation more difficult: Handling and installing heavier heat sinks may require additional equipment or personnel, increasing the complexity and cost of installation.
- Limit design flexibility: Heavier heat sinks can constrain the design possibilities for LED lighting systems, particularly in applications where space or weight limitations are critical. Considering lighter materials or hybrid materials, such as copper-aluminum hybrids, can provide a balance between weight and thermal performance.
Achieving a balance between the weight and thermal performance of the heat sink is crucial for a successful LED lighting solution. Consider factors such as material choice, design optimization, and installation requirements to strike the right balance.
How To Install a LED Heat Sink Properly?
Proper installation of an LED heat sink is essential for ensuring optimal heat dissipation and the longevity of the LED lighting system. Here are some steps to follow when installing an LED heat sink:
- Prepare the LED and heat sink: Clean the surfaces of the LED and heat sink with isopropyl alcohol to remove any residue, dust, or debris that may hinder heat transfer.
- Apply thermal interface material: Apply a thin, even layer of thermal interface material (TIM) to the LED’s contact surface or the heat sink base. This will help fill any gaps between the surfaces and improve heat transfer.
- Mount the LED to the heat sink: Carefully align the LED with the heat sink and press down gently to ensure good contact between the surfaces. In some cases, screws or clips may be used to secure the LED to the heat sink.
- Ensure proper airflow: Install the heat sink and LED assembly in a way that allows for adequate airflow around the fins. This may involve orienting the fins vertically or ensuring there is sufficient space between the heat sink and any nearby components.
- Monitor temperature: After installing the heat sink, it is important to monitor the temperature of the LED during operation to ensure that it remains within the recommended range. If the temperature exceeds the specified limits, adjustments may be required to the heat sink design or installation.
By following these steps and understanding the importance of proper heat sink selection and installation, you can optimize the performance and lifespan of your LED lighting system.
How to Optimize Heat Sink Efficiency?
To maximize the efficiency of a LED heat sink, consider these strategies:
- Optimize heat sink design: Tailor the heat sink design to your specific application, considering factors such as surface area, fin geometry, and material choice. A larger surface area can increase heat dissipation, and a well-designed fin geometry can enhance airflow efficiency. The optimal design may vary depending on whether the application relies on natural or forced convection.
- Use appropriate TIMs: Selecting the right TIM can significantly impact the heat transfer between the LED module and the heat sink. Higher-performance TIMs, such as phase-change materials, can offer thermal conductivities of up to 4 W/m·K, improving the overall efficiency of the heat sink.
- Ensure proper installation: Proper installation and mounting of the heat sink can impact its efficiency. Clean contact surfaces, correct alignment, and even distribution of TIM all contribute to better thermal performance.
- Maintain adequate airflow: Facilitate heat dissipation through convection by maintaining sufficient airflow around the heat sink. This can be achieved by optimizing the spacing and orientation of fins, and in the case of active cooling, selecting the right type of cooling device (e.g., fans or heat pipes) and positioning it for maximum efficiency.
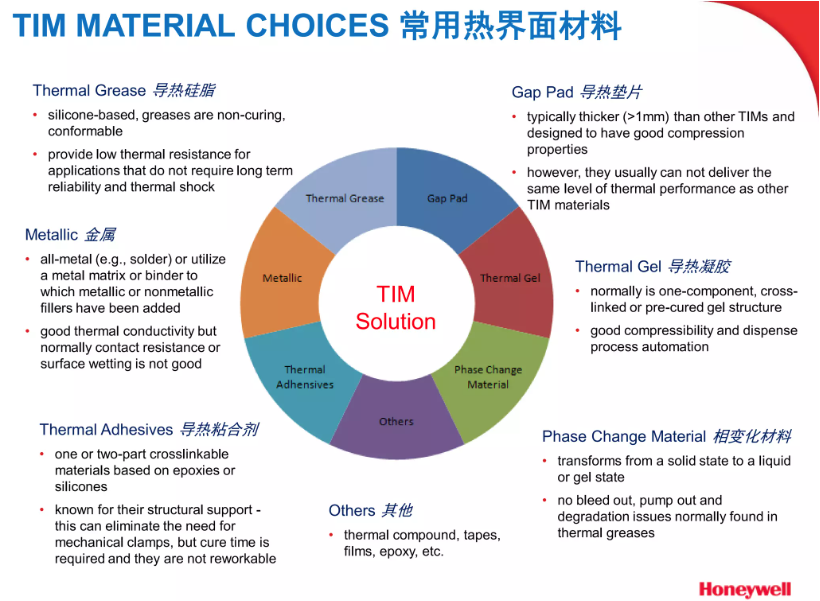
Source: Honeywell
Thermal Simulation and Analysis for LED Heat Sink Design
To optimize the performance of an LED heat sink and ensure its suitability for a specific application, it can be helpful to conduct thermal simulations and analysis during the design process. This can provide valuable insights into the heat sink’s performance under various operating conditions and enable you to make informed decisions about material selection, surface treatments, and other design considerations.
- Thermal modeling: Create a thermal model of the heat sink using specialized software to simulate the heat transfer process and identify potential hotspots or areas of concern within the design.
- Computational Fluid Dynamics (CFD): CFD simulations can provide detailed insights into the airflow and heat transfer patterns around the heat sink, helping to identify areas for improvement and optimize the design for maximum performance.
- Finite Element Analysis (FEA): FEA can be used to analyze the structural integrity of the heat sink and identify potential points of failure or deformation under thermal stress.
- Thermal testing and validation: Once the heat sink design has been optimized through simulation and analysis, it is essential to conduct physical testing to validate its performance under real-world operating conditions. This may involve measuring temperature, airflow, and heat transfer rates in a controlled environment.
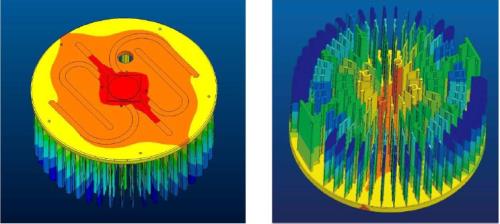
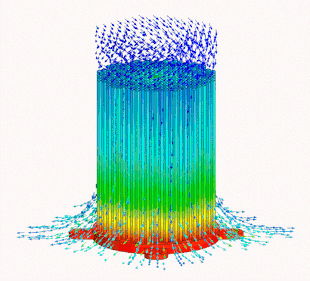
By incorporating thermal simulation and analysis into the design process, you can optimize the performance of your LED heat sink and ensure that it meets the specific requirements of your application.
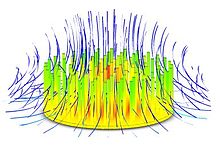
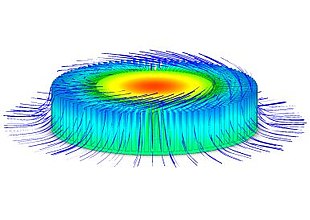
Conclusion
LED heat sinks are a critical component in LED lighting systems, ensuring optimal performance, efficiency, and longevity. By understanding the importance of heat sinks and how they work, you can make informed decisions when choosing LED lighting solutions for your home or business. From selecting the right materials and design to proper installation and maintenance, every aspect of heat sink management plays a crucial role in the success of your LED lighting project. By paying attention to these details, you can enjoy the many benefits of LED lighting, such as energy savings, lower maintenance costs, and a more sustainable lighting solution for years to come.